Temple University’s Historic Renovations at Conwell & Carnell Halls
March 23, 2018
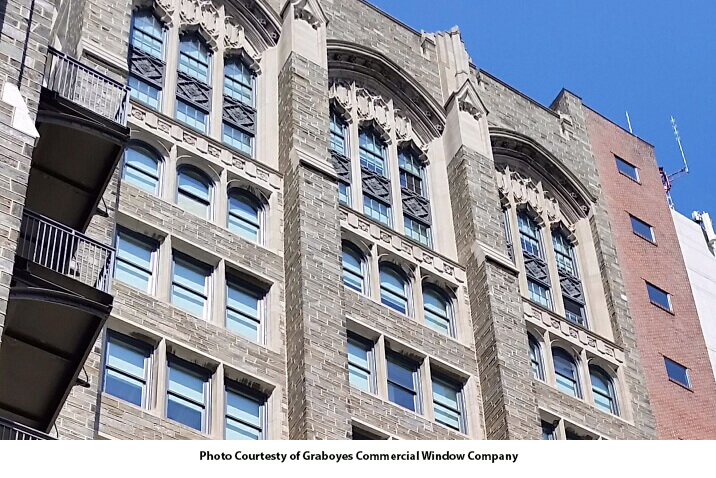
Conwell & Carnell Halls Get Facelift
Once again, Graham has helped to restore some historic buildings on Temple University campus.
We supplied over 600 customized GT2200 Series double hung windows and 114 GT1400 Series fixed windows to satisfy the historic accuracy required. The original steel windows that were in the building, manufactured by the Pomeroy Company, had to be matched for their original historic profiles and sightlines.
Originally built in the 1920s (Conwell Hall in 1922 and Carnell Hall in 1928), the two buildings at a distance look like one. Conwell Hall – named for Temple University’s founder and first President, Russell Conwell – was built in 1922. Carnell Hall was named for Laura Carnell, who started as principal of the Women’s Department in 1893. She soon became the University’s chief administrator as secretary of the Board of Trustees. Called the “Dean of Deans,” Carnell served as associate president from 1925 to her death on March 30, 1929.
Graboyes Commercial Windows Company finished up substantial installation of the windows in the fall of 2017. They have posted more information about the project here.
To find out more about the Graham window products used on this project, contact Bruce Croak, Graham’s marketing manager.
Specifying Windows for Adaptive Reuse
March 8, 2018
Six Things to Know When Specifying Windows
for the Adaptive Reuse of Historic Mills
Are you renovating an historic mill and hoping to secure National Park Service tax credits or other historic review board approvals? Then the following words …
Where D.C. Meets its Water
February 21, 2018
Huge New Development in Washington, DC
Three years after breaking ground, the District’s largest new development project has opened.
Graham played its part by supplying (569) 6800 Series awning windows, (2182) 6800 Series fixed windows, and (137) GT7700 Series …
Graham Window Wall Projects Featured in US Glass Magazine
February 6, 2018
The January edition of US Glass magazine interviewed our National Sales Manager, Mark Hiscock for his insights on window walls and their place in the fenestration market place. The article discusses the differences between window wall and curtain wall and …
Project So Successful, It “Should Be a Model for Future Projects”
January 30, 2018
“Graham did a great job,” says Mark Drake, Architect
Watergate at Landmark, a gated condominium community in Alexandria, VA, recently completed a multi-phase window and door replacement project. It went so well that the condo board president said in …
Artist Lofts, Featured in Retrofit Magazine
January 15, 2018
Artist Lofts, Featured in Retrofit Magazine
The January/February issue of Retrofit Magazine has a feature article on Artist Lofts in Manitowoc, WI. Graham supplied over 300 of its SR6700 Steel Replica Windows in 12 different sizes. Read the full …
“All Pull Together”
December 29, 2017
A bold redevelopment project in Milwaukee Wisconsin’s Harambee neighborhood.
A Neighborhood Institution
The building located at 2821 N. 4th St. has a rich and storied history.
It originally housed the Nunn Bush Shoe Co., but most recently the property …
Kreider Commons Receives Award
December 20, 2017
LEED Project of the Year
Graham is proud to have been part of the Kreider Commons project that has been named LEED Project of the Year by USGBC Central Chapter at the 2017 Forever Green Awards.
In October 2016 we reported …
Graham’s Steel Replica Window Receives Accolade
December 8, 2017
Steel Replica Window Awarded
Graham’s SR6700 Steel Replica Window has been named one of Commercial Architecture magazine’s 2017 Products of the Year.
The December issue of the publication can be viewed in full here.
The innovative SR6700 aluminum …
Lifting the Veil
December 1, 2017
Enthusiasm is building for “The Legacy” in Bay City, MI
The northwest corner of Center and Washington avenues in Bay City is looking like its former self, thanks to a $12 million restoration currently underway.
The Legacy will be …